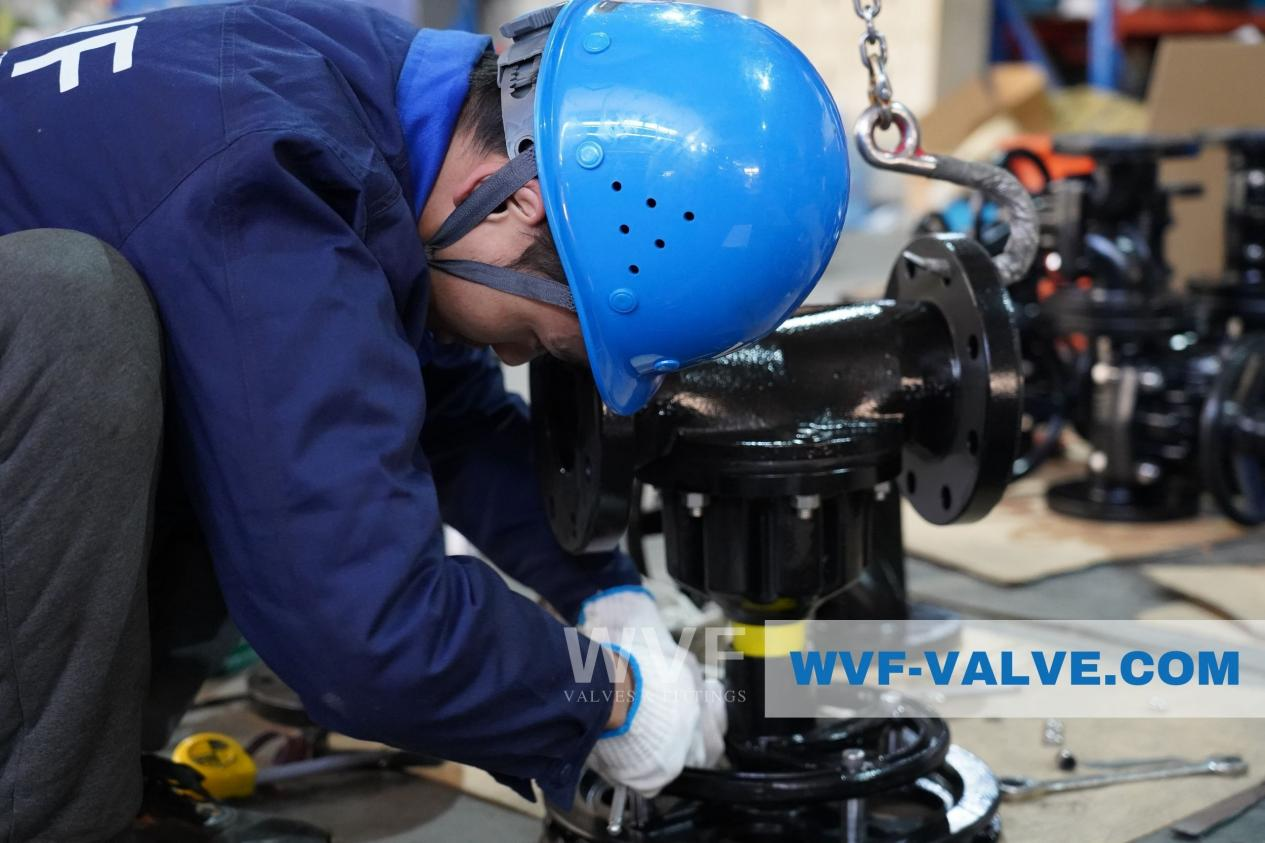
Non-destructive testing (NDT) methods for valves
Nondestructive testing (NDT) is a key technology used to detect internal or surface defects in materials, structures and equipment without causing any damage. NDT methods are essential to ensure the safety, reliability and performance of valves in various industries such as oil and gas, power generation and chemical processing.
- Common nondestructive testing methods
Nondestructive testing of valves involves various techniques to detect defects that may affect the integrity of the valve. These methods include mechanical property testing, chemical composition analysis, and several nondestructive testing methods that do not damage the item being tested. The basic principle of nondestructive testing relies on detecting physical changes in the internal structure of the material due to defects. Common nondestructive testing methods used for valves include:
Radiographic Testing (RT)
Ultrasonic Testing (UT)
Penetrant Testing (PT)
Magnetic Particle Testing (MT)
These methods are used to identify defects such as porosity, shrinkage joints and surface irregularities in cast valve bodies. Radiographic testing is particularly effective for detecting these internal and surface defects due to its high sensitivity and minimal reliance on human factors.
- Importance of Nondestructive Testing of Valves
- Ensure safety
Valves are key components in industries such as petroleum, chemical and power generation, used to control critical systems. Nondestructive testing helps to detect potential defects early, ensure the integrity of the valve and prevent accidents that may jeopardize system safety.
- Extend service life
Regular non-destructive testing can monitor valve wear and assess remaining service life. This enables engineers to effectively plan maintenance and replacements, ultimately extending valve service life and reducing unexpected failures.
- Improve efficiency
NDT provides fast and accurate insight into valve condition, helping to reduce downtime due to misdiagnosis. This can improve operational efficiency and enable smoother production processes.
- Cost savings
Unlike destructive testing, which requires damaging the valve for inspection, NDT is non-intrusive. This means that inspection can be performed without removing or replacing the valve, saving the time and costs associated with repairs and downtime.
- Nondestructive testing methods for valves
- Ultrasonic Testing (UT)
Ultrasonic testing uses high-frequency sound waves that propagate through the material. By analyzing the reflected signal from internal defects in the valve, internal defects such as cracks or voids can be identified.
advantage:
- Detecting internal defects
- Provides accurate thickness measurement
- Radiographic Testing (RT)
Radiographic testing uses X-rays or gamma rays to penetrate the valve material. The level of radiation attenuation can reveal internal defects such as cracks or voids.
advantage:
- High sensitivity to internal defects
- Minimum human error due to straightforward nature of inspection
- Magnetic Particle Testing (MT)
Magnetic particle testing applies a magnetic field to the valve surface. Magnetic particles are then used to identify surface defects such as cracks, which become visible as the magnetic particles collect at the defect location.
advantage:
- Effective detection of surface and near-surface defects
- Quick and easy operation
- Penetrant Testing (PT)
In penetrant testing, a liquid containing a fluorescent or dye penetrant is applied to the valve surface. The penetrant enters tiny surface cracks, and a developer is then used to make these cracks visible.
advantage:
- Simple and cost-effective
- Ideal for detecting surface damaging defects
- Application scenarios of valve nondestructive testing
- Acceptance inspection of new valves Before the valves are put into service, non-destructive testing (NDT) is used to detect any manufacturing defects and ensure that the valves meet the required quality standards.
- Regular Inspection of Valves in Use For valves already in use, regular nondestructive testing can help monitor their operating status and detect potential problems before they lead to system failures or safety hazards.
- Emergency Inspections After an Incident If a valve leak or failure occurs, non-destructive testing (NDT) can be used to assess the extent of the damage and help determine if the valve needs repair or replacement.
- Re-inspection after maintenance After the valve is repaired, non-destructive testing (NDT) is used to verify the effectiveness of the repair and ensure that no other defects exist.
in conclusion
Nondestructive testing (NDT) plays a vital role in ensuring the safety, reliability and longevity of valves. By using techniques such as ultrasonic, radiographic, magnetic particle and penetrant testing, engineers can identify defects without compromising the integrity of the valve. Regular use of NDT can help improve operational efficiency, extend valve life and reduce maintenance costs. As industrial automation continues to advance, NDT technology will play an increasingly important role in maintaining the reliability of valves in critical systems.
Understanding and implementing NDT methods is essential for engineers and technicians in industries where valve performance is critical to system safety and efficiency.